Introduction
In an era where connectivity is key, the production of Cat 6/7 LAN cables is a lucrative business venture. These cables are essential for high-speed networks, making the setup of a manufacturing plant a strategic investment. This guide outlines the necessary equipment and steps to establish a factory capable of producing premium network cables.
Embarking on the journey of crafting high-quality LAN cables involves a meticulous process, each step contributing to the cable’s reliability and performance. Let’s delve into the intricacies of network cable manufacturing, unraveling the five key steps that shape these essential components of modern connectivity.
Mastering the Art of Network Cable Manufacturing in 5 Crucial Steps
1. Wire Drawing Processes: Laying the Foundation
The journey starts with wire drawing, where copper wire undergoes a transformative process. Drawing through dies reduces its diameter while maintaining volume. Lubricant-cooled dies prevent overheating, producing a coil of 10, 12, or 14 AWG copper wire. Subsequent transfers and draws refine the wire’s size, followed by annealing to ensure desired properties and performance.
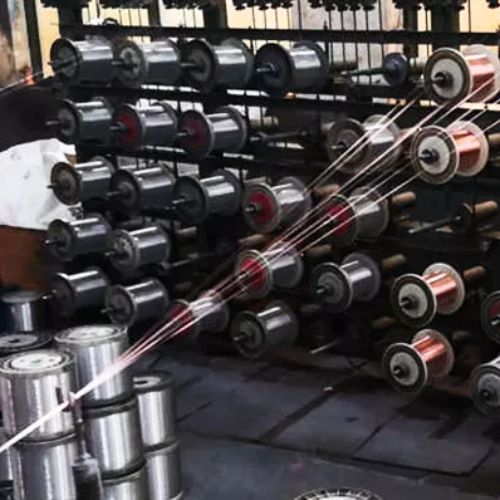
2. Applying Insulation: Protecting the Core
Wire extrusion takes center stage, where plastic insulation is meticulously applied through an extruder. High-density polyethylene pellets melt, homogenize, and coat the preheated copper conductor. This insulation not only shields the wire but also contributes to improved transmission performance, including insertion loss.
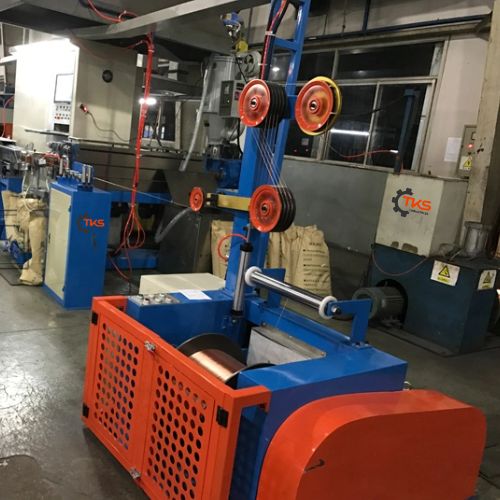
3. Wire Twisting and Stranding: Crafting Pairs for Performance
Insulated wires undergo twisting into pairs with unique lengths, minimizing crosstalk and interference. Electrical testing ensures the pairs meet quality standards, and pre-twisting equipment enhances conductor control. This step is crucial for achieving optimal return loss and impedance performance, integral to noise reduction in the twisted-pair geometry.
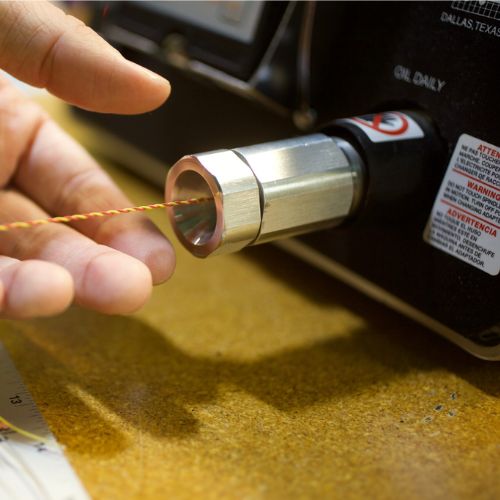
4. Twinning Process: Unity in Diversity
The twisted wire pairs unite to form a multi-unit cable core, promoting flexibility and controlling electrical interference. This stage is vital to prepare the cable for subsequent processes, setting the foundation for its functionality in diverse applications.
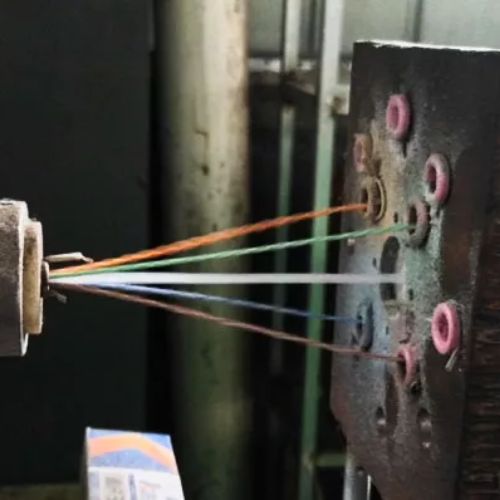
5. Jacketing: Shielding for the Long Haul
The cable core undergoes jacketing, incorporating gel-filling, armoring, and extrusion of the outer cable jacket. Gel-filling ensures void-free insulation, and armoring adds protection against external threats. The outer jacket, often made of low-density polyethylene, shields the cable from environmental factors. Metal sheathing may be added for grounding or mechanical protection.
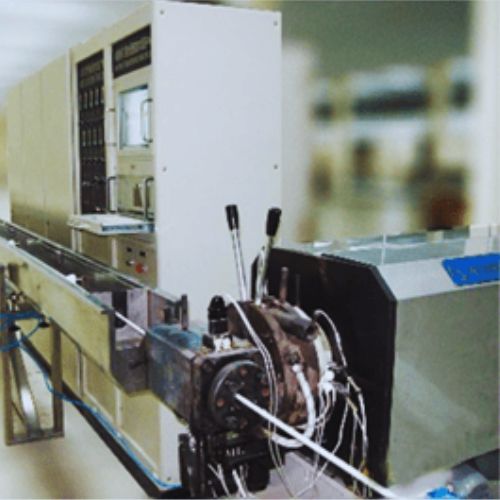
Cables Testing: Ensuring Perfection
The finalized cable undergoes meticulous testing. Physical inspection verifies the cable’s construction, ensuring correct placement of units and spare pairs. Electrical tests, including continuity checks and core-to-sheath evaluations, guarantee the cable’s integrity. Random tests cover mutual capacitance, unbalance, and resistance, ensuring each cable meets stringent quality standards.
In conclusion, these five steps encapsulate the art and science of network cable manufacturing at TKS Industries. From drawing the initial wire to the comprehensive testing of the final product, each stage is a testament to precision, innovation, and commitment to delivering cables that power seamless connectivity in the digital age.
Machinery Requirements for Establishing a Cat 6/7 LAN Cable Manufacturing Plant
A state-of-the-art manufacturing setup is crucial for producing high-quality LAN cables. The essential machines needed are:
1) LAN CABLE EXTRUDER LINE: This machine is the workhorse of the factory, extruding insulation around the conductive core of the cable.
2) TRIPLE TWIST BUNCHER: It intricately twists the wires into pairs, which is essential for reducing crosstalk and maintaining signal integrity.
3) LAYING MACHINE FOR PAIRS & CROSS SEPARATOR: This equipment arranges twisted pairs into the cable’s precise layout and inserts a cross separator to maintain structure and reduce interference.
Why Choose TKS Industries?
Innovation: TKS Industries leads in wire processing innovation, incorporating the latest technological advancements for superior cutting and stripping performance.
Reliability: Our Wire Cutting and Stripping Machines are well known for reliability. Built for consistency, they ensure the integrity of your wire products.
Custom Solutions: Benefit from our ability to provide tailored wire cutting and stripping solutions, meeting the unique requirements of your wire processing operations.
Elevate your wire processing efficiency with TKS Industries’ Wire Cutting and Stripping Machines. Contact us today to explore how our advanced technology can enhance the precision and speed of your wire cutting and stripping operations.